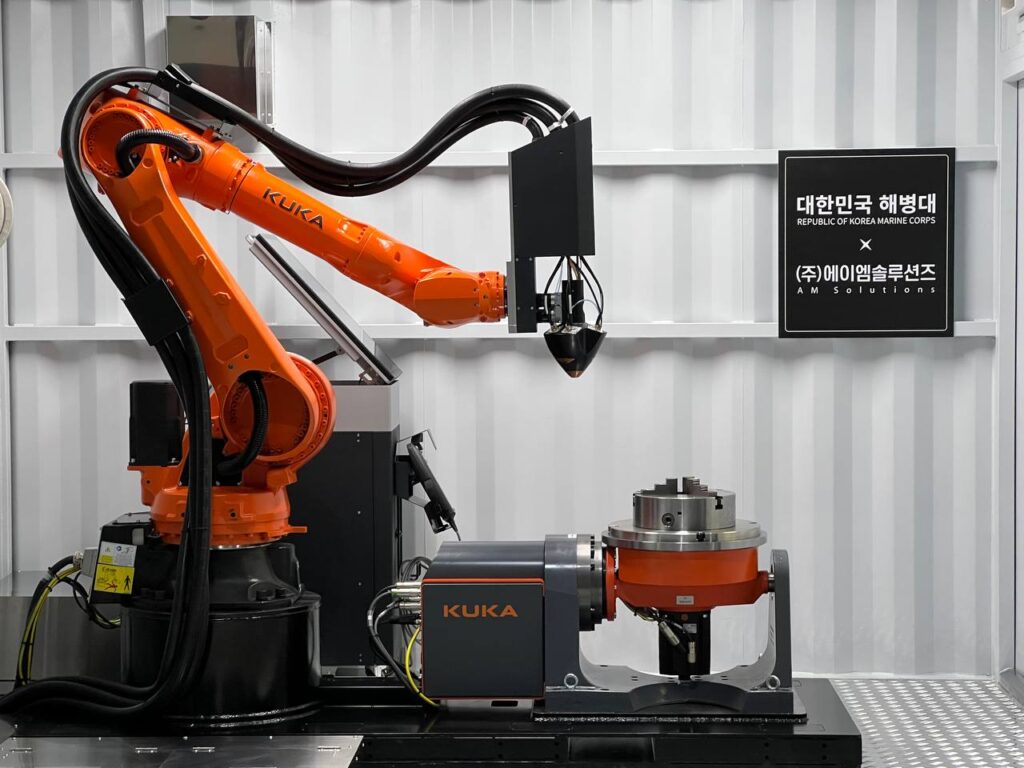
Meltio, in partnership with AM Solutions, has introduced its certified wire-laser metal 3D printing technology to the Korean Army, enhancing defense logistics with cost-effective, on-demand manufacturing and repair solutions.
As part of this initiative, the Meltio metal 3D printer employs the Laser Wire Directed Energy Deposition (LW-DED) method. This advanced metal Additive Manufacturing (AM) technology works by melting metal wire with a laser beam and layering it to form a three-dimensional structure. Compared to other metal AM techniques, DED technology significantly reduces material waste, making it a cost-effective solution for manufacturing. Meltio systems are capable of reliably producing metal parts using Stainless Steel, Titanium, Copper, Inconel, and a wide range of other metal alloys.
This achievement was made possible through a collaboration between Meltio and AM Solutions, extending the initiative to the Korean Army.
Additionally, this marks the first time the Army of the Republic of Korea has decided to integrate metal additive manufacturing solutions for spare parts and repairs, gaining autonomy over conventional and more costly manufacturing processes.
According to an article published by the South Korean magazine Kookbang and Meltio’s partner, AM Solutions, the Marine Corps Logistics Group is the first in the entire military to use robot-based metal 3D printers for logistics support.
This advancement enables the rapid manufacturing of discontinued or hard-to-source repair parts. Field maintainability is expected to improve significantly, as the system can be relocated using a crane or forklift
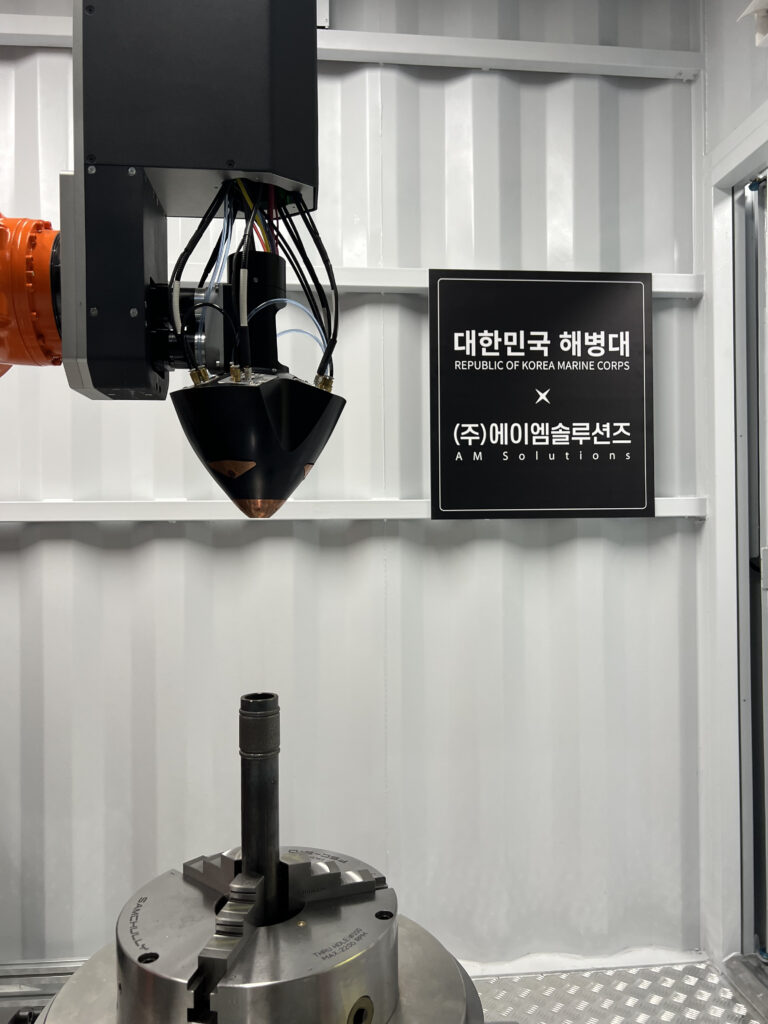
Thanks to AM Solutions, Meltio offers the Korean Army its unique Meltio Integration Kit for Industrial Robots. This system turns an industrial robot arm into a metal 3D printing system eliminating inherent size constraints, allowing for large-scale metal 3D printing, including complex geometries. It is the ideal platform for large-scale 3D printing, repair, cladding, and adding features to existing parts.
The Meltio Engine seamlessly integrates with nearly any robotic arm manufacturer and interface available on the market. Its Meltio Space slicer software for robotic systems is fully compatible with ABB, Kuka, Fanuc, Yaskawa.
Over the next two years, the Marine Corps Logistics Group plans to enhance its maintenance support capabilities by increasing operational proficiency and expanding field equipment, including mobile metal precision processing machines and generators
Adam Hourigan, Meltio Sales manager for APAC region, commented, “The defense sector is strategic for Meltio. Our technology is being validated by armies all over the world and for us it is very positive that thanks to collaboration agreements with relevant partners in Asia such as AM Solutions we are able to help with our different 3D metal wire welding printing solutions the army of the Republic of Korea to gain autonomy in manufacturing and creating metal parts in a reliable and sustainable way.”
Lieutenant Colonel Kim Seong-nam of the Republic of Korea, commander of the maintenance battalion, also said, “The introduction of metal 3D printers is significant not only for reducing operation and maintenance costs, but also for preventing delays in maintenance schedules due to limited procurement of repair parts. We will maintain the best logistics support system to enable stable maintenance support.”
Daejung Kim, AM Solutions CEO, stated, “The successful introduction of Meltio’s outstanding technology into the Republic of Korea marks a significant milestone in local manufacturing innovation.”
Kim also conveyed that this entry into the defense sector is just the beginning, and through a continuous partnership with Meltio, they aim to lead the Republic of Korea’s advanced industries in other sectors requiring additive manufacturing.
On the 19th of February, the Marine Corps Logistics Group announced, “We have introduced a container-type mobile metal 3D printer to quickly and smoothly provide logistics support, such as manufacturing parts in-house to cope with the limited procurement and discontinuation of repair parts for Marine Corps-specific equipment, including the amphibious assault armored vehicle (KAAV).”